
Co-Injection Hot Runner
A co-injection hot runner is an injection molding melt distribution system designed to enable the simultaneous injection of two different materials through a single gate into a mold. In a typical setup, a 'core' material is enveloped by a 'skin' material. This dual injection process is controlled and precise, ensuring consistent and high-quality products.

Post-Consumer Recycled (PCR) plastics can be used as the core material in co-injection molding processes. This is especially valuable for thick-walled products, where the outer ‘skin’ layer can be a virgin or high-quality material, while the inner ‘core’ layer is made from recycled material. This allows for significant savings on material costs while producing eco-friendly products.
Material Efficiency and Cost Savings:
By using PCR material as the core, manufacturers can significantly reduce the usage of more expensive virgin materials. This is a strategic cost-saving measure while maintaining product quality and appearance, as the outer layer remains pristine.
Enhanced Product Properties:
Co-injection molding with a PCR core can improve the structural integrity of thick-walled products. The PCR material can provide strength and stability, while the outer skin ensures the product has a high-quality finish.
Expanding the Use of PCR:
Traditionally, PCR materials were challenging to incorporate into high-quality products due to their appearance and properties. Co-injection hot runners break down this barrier, enabling the widespread use of recycled materials in premium products.

Reduced Waste and Resource Conservation:
By using PCR material, co-injection hot runners promote the re-use of plastic waste, thereby reducing the need for new raw material production and minimizing waste sent to landfills.
Sustainable Production:
Co-injection molding with PCR supports companies in their sustainability goals. It enables the creation of new products from old, contributing significantly to a closed-loop, or 'circular,' production model.
Market Opportunities:
As consumer demand for sustainable products grows, manufacturers using co-injection hot runners to incorporate PCR materials are well-positioned to access new market opportunities. They can offer products that meet high environmental standards, which is increasingly becoming a competitive advantage.
Regulatory Compliance:
As regulations around the use of recycled materials in production become more stringent, co-injection hot runners that allow for the seamless integration of PCR materials can help manufacturers stay ahead of the curve and maintain compliance.
Revolutionizing the Packaging Sector
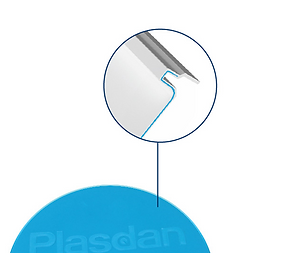
Co-injection hot runner systems are redefining the way packaging is produced. By facilitating the simultaneous injection of two distinct materials into a single mold, these systems empower packaging manufacturers to create products that are not only aesthetically pleasing but also more sustainable and cost-effective.
​
Specific Application: Sustainable Barrier Packaging
In the packaging sector, co-injection hot runners are commonly used to create high-quality barrier packaging. This involves encasing a recycled or biodegradable core material with a virgin polymer, often to produce containers or bottles with excellent barrier properties against oxygen, moisture, and other environmental factors. This ensures product integrity and extends shelf life.
​
Resource Efficiency and Lower Costs: Co-injection hot runners allow the core layer of a package to be formed using recycled or lower-cost materials while maintaining the superior characteristics of the outer layer. This efficient use of materials translates directly into cost savings for manufacturers.
Enhanced Performance and Quality: The two-material system ensures packaging with excellent structural rigidity and barrier properties. The outer layer ensures a high-quality aesthetic finish, and the inner layer can be engineered to provide specific functionalities, such as UV protection or enhanced oxygen barrier properties.
Reduced Material Weight and Thickness: Co-injection hot runner systems enable the production of lighter and thinner packaging without compromising on quality or performance. This reduction in material usage is not only cost-effective but also lowers the carbon footprint of the packaging.
​
Contribution to Sustainable Packaging:
-
Promoting Circular Economy in Packaging:
-
By allowing the integration of recycled or biodegradable materials, co-injection hot runners play a critical role in developing packaging solutions that are in line with circular economy principles.
-
-
Meeting Sustainability Goals and Regulations:
-
As the demand for sustainable packaging options increases and regulations become more stringent, co-injection hot runner systems are a solution for manufacturers aiming to stay ahead of these trends and fulfill their environmental responsibilities.
-
-
Consumer Appeal and Market Differentiation:
-
With growing consumer awareness about environmental issues, sustainable packaging is more than a trend; it’s a market expectation. Co-injection hot runner systems allow manufacturers to meet this demand, offering a clear competitive advantage in the marketplace.
-
Get a Quote
Let's talk about your project